Munters´ mass transfer solutions helped one of the top three largest producers of glycerin and fatty acid in India reduce utility consumption by 20% and decrease their environmental impact.
Quick facts
- Customer: Producer of glycerin and fatty acid
- Location: Western India
- Tower Name: Pre-cut distillation column
- Tower Diameter: 800 mm
- Mass Transfer Equipment: Structured packing (ME-II 250 Y) and tower internals
Background
The customer is one of the top three producers of glycerin and other integrated components of fatty acids in India. Process overview The fatty acid distillation plant has been designed and installed to achieve desired product purity and quality at a minimum cost while also taking care of variations in input feed composition. Customer Requirements: - Enhance capacity to handle feed with variable feed stocks - Resolve the product purity problem - Reduce energy consumption Problem analysis After detailed study of the fatty acid distillation plant and a thorough hydraulic rating of existing tower internals, several problems were noted that were restricting capacity: - Polymerization or chocking of random packing - Excessive pressure drop in packing and internals - Poor feed distributor due to improper selection of distributor - Incorrect elevation of internals Solutions provided Munters recommended changing random packing to structured packing, thus allowing better contact of liquid and vapor and ensuring low pressure drop. The tower internals were also redesigned to suit the modified packing. The liquid distribution system was also redesigned by modifying the existing pipe arm distributor and including a new liquid distributor to ensure efficient liquid distribution on the packed bed. Enough space was provided for proper disengagement of vapor from liquid. Results achieved The column is now working satisfactorily with 30-40% increased capacity and 20% reduced utility consumption. At the top of the columns, the client achieved removal of C6-C10 fatty acid impurities with the slippage of C12 fatty acid reduced it to =< 1%. At the bottom of the columns, the client achieved desired product purity and slippage of C10 fatty acid impurities to <=1%.
Quick facts
- Customer: Producer of glycerin and fatty acid
- Location: Western India
- Tower Name: Pre-cut distillation column
- Tower Diameter: 800 mm
- Mass Transfer Equipment: Structured packing (ME-II 250 Y) and tower internals
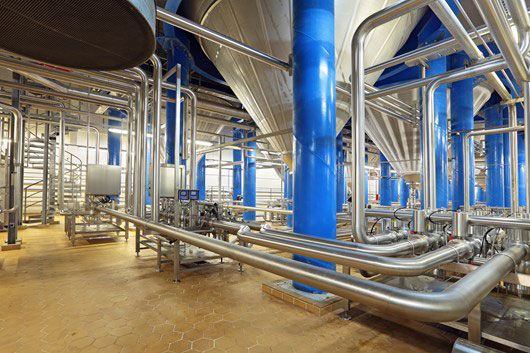
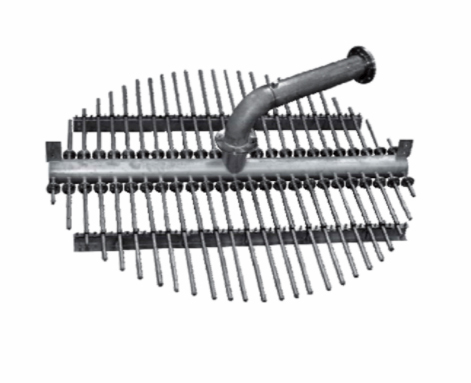
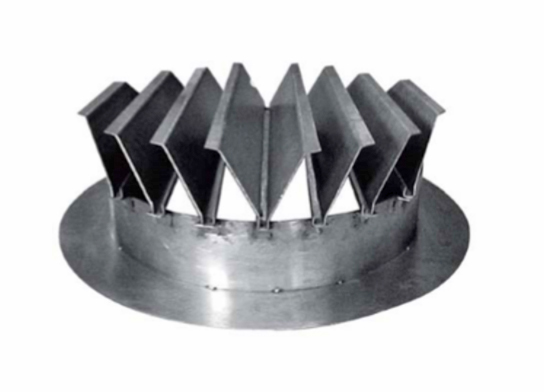