Ahlstrom-Munksjo is one of the world’s leading players in sustainable and innovative fiber-based solutions, with 8,000 employees and 45 plants in 14 countries. Electrotechnical insulation manufacturing of paper takes place at the Jonkoping, Sweden plant. This technical paper is used in the insulation of high-voltage cables, transformers and bushings. Ahlstrom-Munksjö had been successfully operating Munters dehumidification equipment for climate control in one of their laboratories for a number of years, until the need arose to update the equipment.
Quick facts
- Superior technical knowledge
- Only one supplier during installation
- Trustworthy service partner
- Fast response from Munters service team
Strictly controlled climate conditions all year round
The lab thoroughly tests the paper material, ensuring quality to comply with ISO standards. The climate conditions in the lab are demanding and have very narrow margins. The relative humidity has to be kept constant at 50% RH, +/-2% and a temperature of 23°C with a margin of only +/- 1°C. Ahlstrom-Munksjö trusted Munters to supply a Turnkey solution, supplying not only the air treatment system needed to fulfill the strict demands, but also the lab construction and interior, which included, walls, ceiling, floors and lightning. Ulrik Persson Munksjö, Project Engineer: “’In this project we were in need of a partner that would fully understand our needs. A partner with the technical knowledge and skills that was able to critically review and discuss the technical details of the full lab interior. We got that with Munters.”
Trustworthy and always understanding the need for fast response
A Munters ML270 Plus system was designed to meet the demands to create and maintain the strict climate conditions required. The system was built around a ML270 dehumidifier and configurated with a post heater, post cooler and humidifier. All built into one system on a common base frame, controlling both temperature and humidity. The system automatically adapts to the fluctuating ambient air conditions, ensuring a constant climate in the lab all year round. Lab construction and installation of the air treatment system took place as planned, meeting all agreed upon deadlines. “Everything worked out smoothly and Munters proved to be a trustworthy supplier, always living up to their promises. After start-up and commission of the full installation, we now enjoy the service team´s quick response whenever we have questions or need support. Munters is always prompt in their response, understanding our critical situation.” The equipment is covered by a ServiceCaire™ maintenance agreement, leaving all maintenance to Munters. “Logging the climate in the lab every day we can confirm that the solution supplied by Munters lives up to our expectations and demands” Ulrik Persson added.
Quick facts
- Superior technical knowledge
- Only one supplier during installation
- Trustworthy service partner
- Fast response from Munters service team
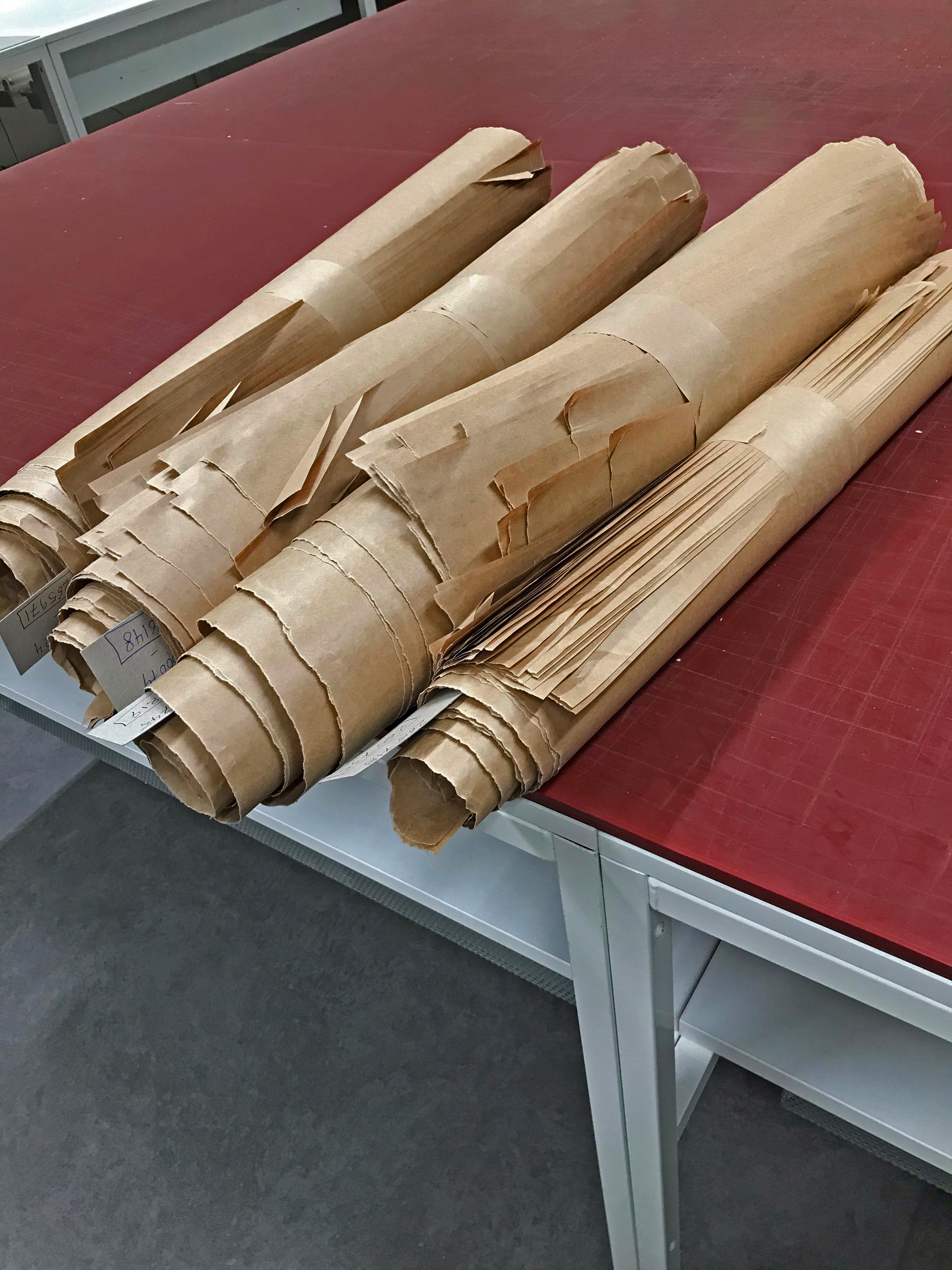
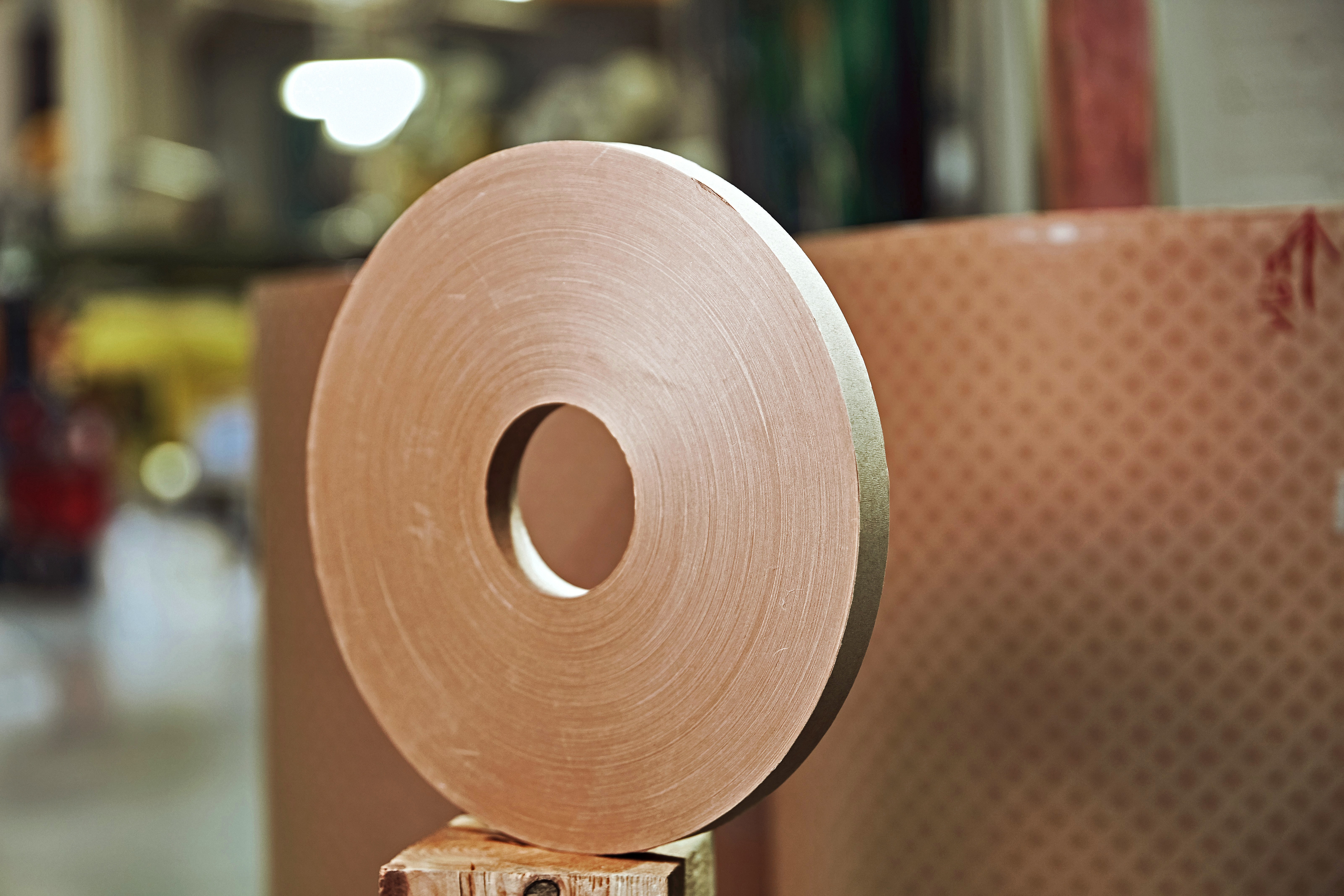
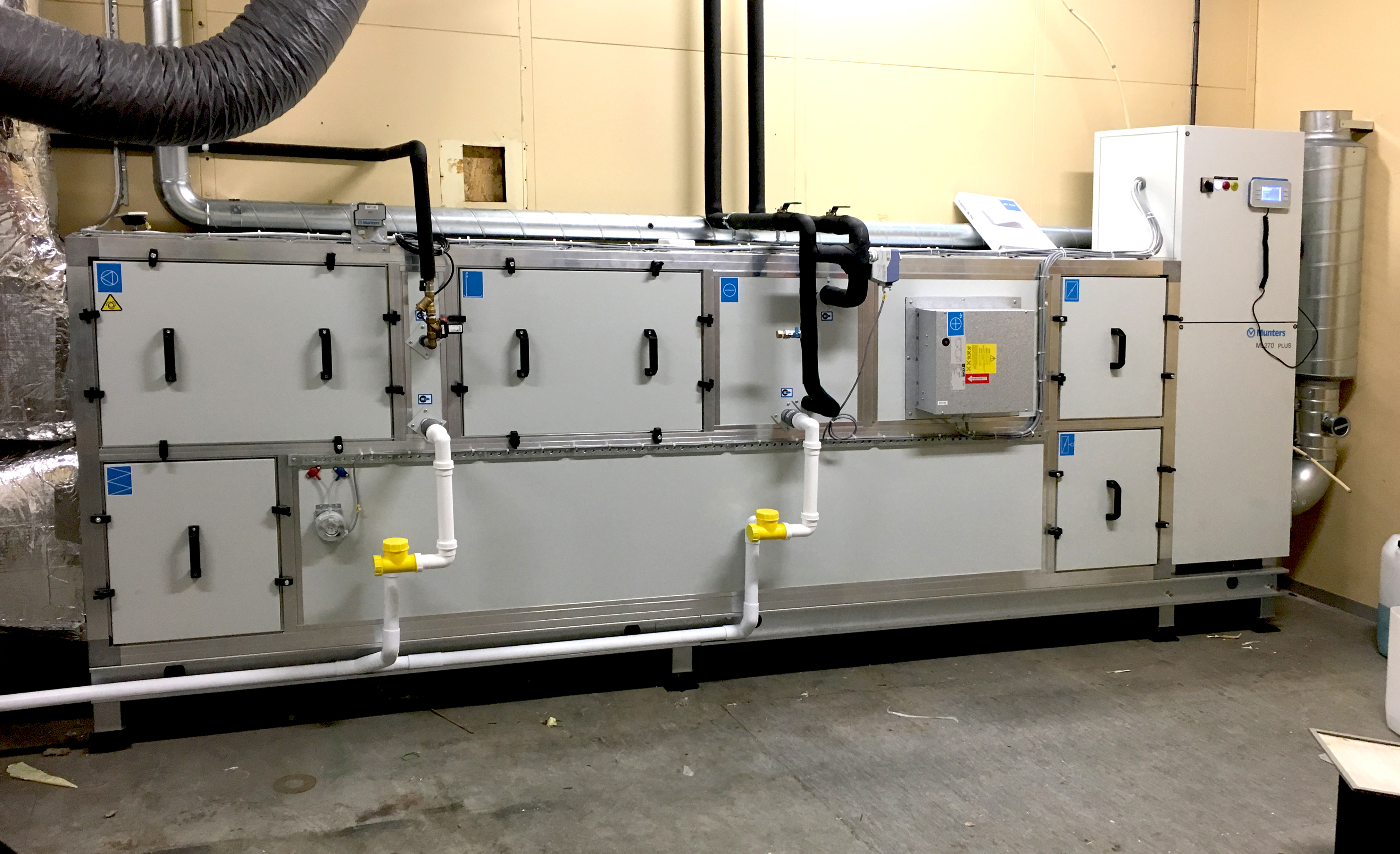