Product cooling
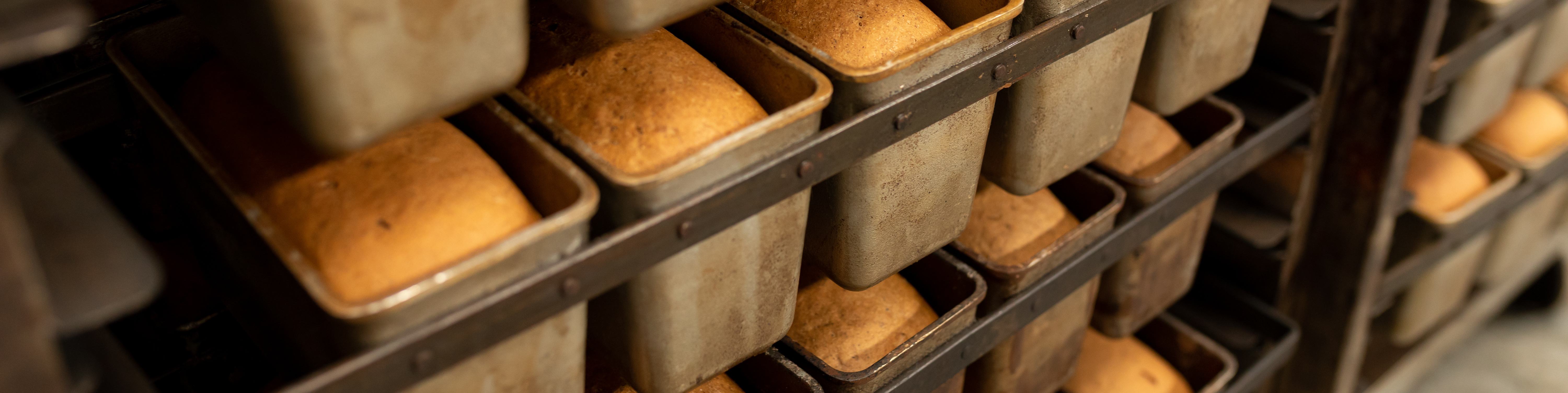
Conditions and challenges
The manufacturing cooling process often means products are too hot for packing and need to be cooled. During the cooling process the product may re-absorb moisture from the cooling air. Re-absorption of moisture can soften products making them less desirable and reducing shelf life.
What we can do for you
We can help dehumidifying the air to maintain relative humidity at or lower than the equilibrium which prevents re-absorption of moisture. With correct tunnel conditions there is no risk of moisture corruption, or reject product and improved product consistency. This ease your planning of production schedules as tunnel/coolers can operate at the same temperature year-round.
Our solution
Munters desiccant dehumidification system operates below 10°C, preventing condensation occurring by removing moisture from the air and creating a dew point below 4°C. At this level, even the cooling coils, the tunnels/coolers coldest surface, are immune to condensation. Our solution helps increase your production by lowering temperature without the risk of condensation.
Your benefit
- Prevent moisture re-absorption
- Uniform quality
- Less throw away
- Improve product consistency
- Reduce mold growth
- Extend period between cleaning