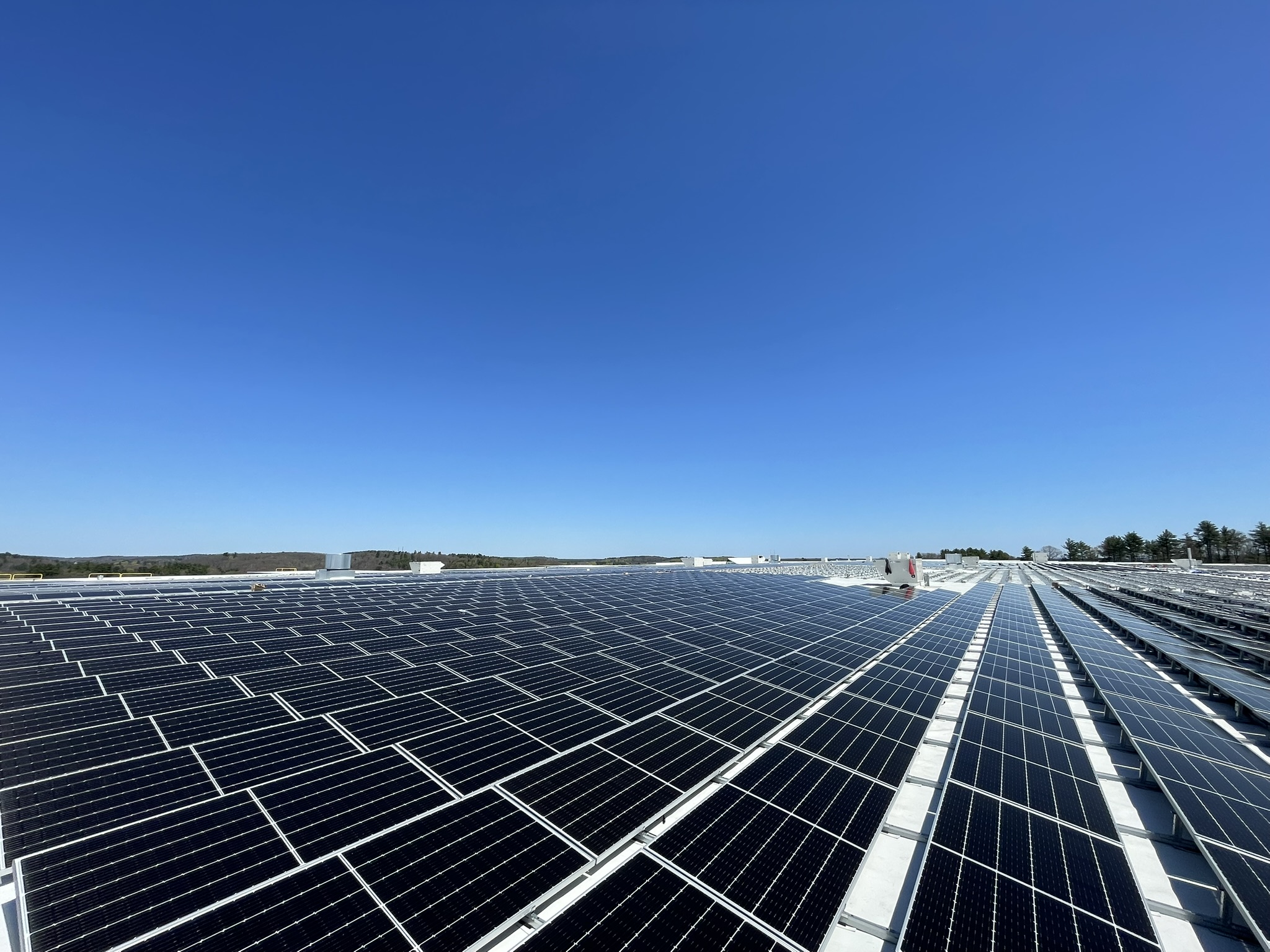
Built to last. Designed for the future
May 26, 2025
Amesbury is a charming city in the US state of Massachusetts, located about 60 kilometers (approx. 38 miles) north of Boston. With a population of 18,000 people, the city offers a small-town feel combined with a vibrant local economy. For more than 60 years, Munters – the city’s largest employer – has had a presence here.
As a sign of its continued commitment to Amesbury and its employees, Munters will inaugurate a new state-of-the-art facility with a focus on sustainability on May 22, 2025. As a Munters flagship facility, it represents a milestone for both the company and the city. In line with the ambition to reduce emissions related to the use of the company’s products and its own operations, it will be powered entirely by renewable energy and have all the latest green technologies to be as energy efficient as possible.
We sat down with Andrew Cook, Senior Vice President for the Americas, business unit AirTech, to learn more.
The facility has been built with a strong focus on sustainability. Can you briefly share the background behind that?
Supporting the goals of the Paris Agreement to limit global warming to 1.5 degrees C (2.8 degrees F) is a strategic priority for Munters.
As this was a greenfield project, we had an opportunity to rethink all of our operations and incorporate multiple innovative energy-saving solutions that will also generate a significant return on our investments.
The HVAC system was designed to provide comfortable heating and cooling while minimizing energy usage. How will that work?
Air-sourced heat pumps powered by renewable electricity will provide cooling in the summer and heating in the winter.
To enhance their efficiency, we’ll be using HVLS (high volume low speed) fans to prevent air stratification and economizers to balance indoor and outdoor air temperatures. During the heating season, we’ll also be capturing and recirculating waste heat from our test units and some of our production processes.
Where will your renewable electricity come from?
We are installing a 2.8-megawatt (3.8 million kilowatt hours) solar array on our roof. This system will cover 45% or more of our annual electricity needs and is enough to power over 350 homes. When the factory isn’t operating, the power will be fed back into the local grid. This will be the first Munters location to have its own solar array.
For the remainder of our energy needs, we’ll purchase renewable electricity from a local energy provider.
How will you save electricity from lighting in the facility?
Our lighting system will use “smart” lights with customizable controls and motion sensors. This will allow us to manage lighting based on needs and zones. Lighting levels are automatically adjusted based on activity in each zone.
Incorporating natural light to save additional energy and enhance our working environment was also a priority. The building’s perimeter walls are lined with windows and the central atrium has a large skylight which faces north to bring in light without the heat.
Have you made any improvements to the production line itself?
Previously, our processes ran on natural gas, and we’ve now electrified all of them. The three areas that consumed the most energy were our corrugators, paint booth and ovens. To further reduce energy usage, we had to come up with some innovative solutions.
One example was finding a paint booth supplier willing to design and build an all-electric system. We worked with our supplier on over 30 iterations to find a design that worked. In the end, we ended up with a solution that incorporated our heat exchangers and a recirculation system. Thanks to these efforts, we were able to reduce the total energy usage of the paint booth by 95% without compromising production. Plus, the new design was a safety and comfort enhancement for our employees.
By incorporating our own heat exchangers into our other processes, we’re able to capture 75% of all waste heat and reuse it.
How do we leverage automation to optimize production?
Incorporating automation was a significant part of enhancing our employee safety, reducing waste, and increasing efficiency. A good example is our new Salvagnini flexible manufacturing system, which combines several previously manual metal fabrication processes, into one automated system.
Another goal of the facility was to be “smart factory” ready. All of our equipment has the ability to be networked and remotely monitored, allowing us to achieve greater operational efficiencies, and tie into our Energy Management System (EMS).
What is the Energy Management System (EMS) – what does it do?
The energy management system (EMS) is how we’ll reduce energy usage in the facility. It monitors all energy consumption throughout the building – everything from our HVAC system to production equipment is connected.
This allows us to monitor trends, identify inefficiencies, and prioritize energy usage. For example, if we notice a certain process uses a lot of electricity intermittently, we could schedule it to run during a time when our solar panels were producing the most power.
Munters has been present in Amesbury for over 60 years and has a close collaboration with the local community. Tell us a bit about it.
Munters has deep roots in Amesbury. Originally founded by US Navy Commander Oliver Colvin, CargoCaire has been in Amesbury since the 1940s. Commander Colvin worked with Carl Munters to perfect the desiccant rotor, and CargoCaire was fully integrated into Munters in the 1970s.
Munters has had a consistent presence in Amesbury and is the city’s largest employer. About a third of our employees are located in the area, and maintaining our presence in the community was a top priority when we were evaluating locations for our new site.
A scholarship is awarded every year – can you tell us more about this initiative?
The Munters scholarship is awarded to two high school seniors living or studying in Amesbury. Each award is $5,000 and is to support students pursuing higher education in STEM, sustainability, or HVAC programs.
The scholarship was created as part of our commitment to Amesbury and helping to build the next generation of talent in our industries.
What are you most looking forward to with the facility in Amesbury?
To me, this is more than just a new factory. It’s a welcoming and inclusive environment for our existing and future employees. It’s a leap forward for us to better serve our customers. And we’ve achieved our goal of staying in Amesbury – prepared to drive our future growth and success.
Quick Facts
Number of employees: ~ 350
Manufacturing: The factory will produce systems, components, and service for industrial dehumidification applications in the North American market.
Facility: 40,000 m²
Major sustainable initiatives: Net zero emission from operations. The building is powered entirely by renewable energy.