Munters supported a leading pharmaceutical producer meet environmental regulations and helped increase plant capacity by 50%.
Quick facts
- Customer: A leading pharmaceutical company
- Location: Western India
- Tower name: Extraction column
- Tower diameter: 700 mm. four packed beds - each 3 meters high
- Mass Transfer Equipment: Random packing (Medal-Pak) and liquid-liquid extraction internals
Background
The client has been in the pharmaceutical industry for three decades, and is a major producer of chemicals and drugs. Process overview In one of their propriety processes for antibiotic manufacturing, the aqueous effluent from the plant contained significant amounts of phenylacetic acid, leading to loss of raw material and problems in the effluent treatment plant (ETP). This was a major concern since it violated environmental regulations. Customer requirements - Provide complete process solution for eliminating phenylacetic acid loss - Optimize existing capacity and accommodate future capacity enhancements plans - Economize proposed project costs by utilizing existing spare column Problem analysis The client had used mixer settlers to extract the phenylacetic acid in toluene, which was not delivering the desired results. Solutions provided Installation of distillation or extraction column was identified as a possible solution for removing the phenylacetic acid from the effluent stream. After collecting data from lab scale experiments on distribution coefficients of phenylacetic acid in water and toluene, a detailed study of the entire system was done. The following was concluded and recommended: - Application of liquid-liquid extraction - Selection of efficient & latest generation Medal-Pak #25 as a contacting media - Selection and design of liquid-liquid extraction internals - Selection of packed height to match required HETP The tower internals were designed and manufactured along with random packing. The random packing and tower internals were installed and commissioned. Results achieved The initial phenylacetic acid concentration in the effluent stream was reduced to 100 parts per million (ppm) level and the plant capacity was increased by 50%.
Quick facts
- Customer: A leading pharmaceutical company
- Location: Western India
- Tower name: Extraction column
- Tower diameter: 700 mm. four packed beds - each 3 meters high
- Mass Transfer Equipment: Random packing (Medal-Pak) and liquid-liquid extraction internals
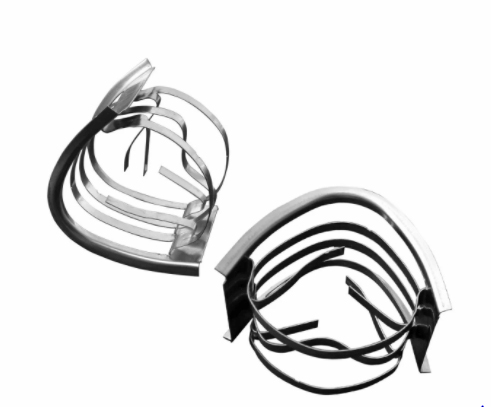
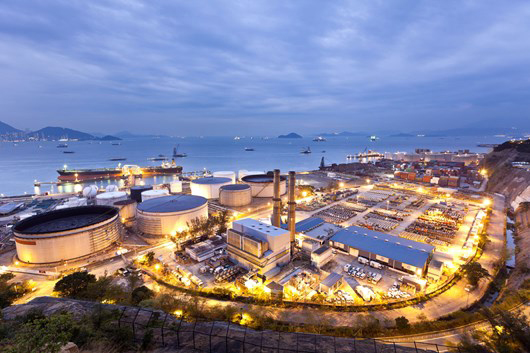
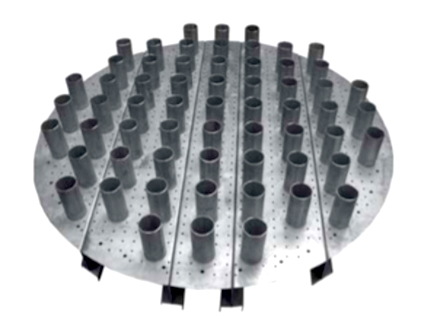